Etihad’s poultry processing plant includes two 15.000 bph lines. This means two totally separated processes, with every department doubled. Two complete ATLAS systems will handle live bird supply, meaning a capacity of 30,000 bph. According to the halal rules, the actual slaughtering must be done manually, while the broilers are facing Quibla. Performing a manual kill cut at a line speed of 15,000 bph is difficult. Therefore, performing a humane process, the two conveyor lines are split again to form four lines of 7,500 bph each, all making a 45-degree bend to face Quibla after the Marel 400Hz Water Bath Stunners.
Etihad, a greenfield project without boundaries
A complete Iraqi ‘poultry city’ in a 565 km2 desert area
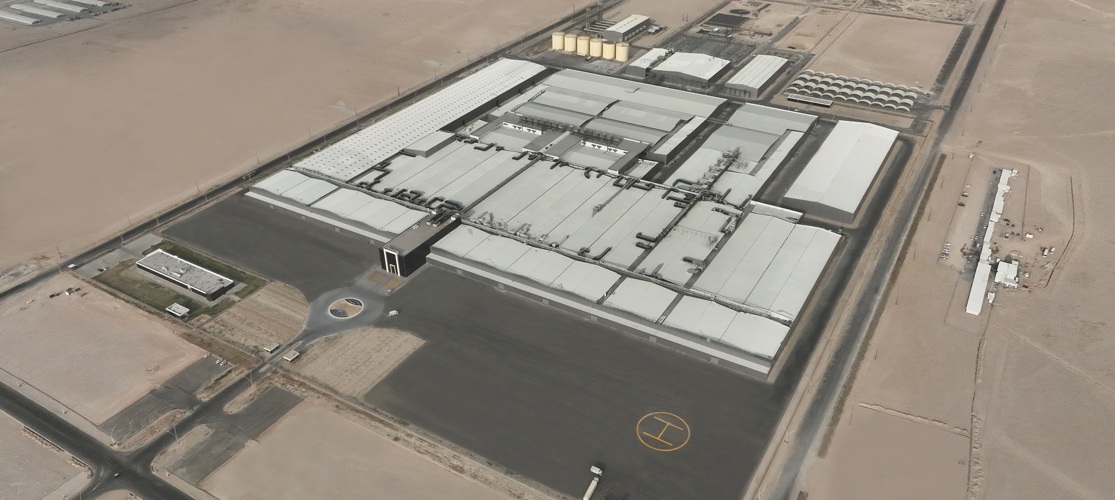
On an almost unimaginably vast site, the Iraqi company Etihad established a completely new ‘poultry city’. Part of this project is the processing plant, fully equipped by Marel. In fact, it’s about two full-blown, separate 15,000 bph factories next to each other. In addition, Marel also supplied an elaborate convenience food line and a 4.000 bph parent/layer line to process sustainable meat coming from parent birds and layer hens as input for mainly further processed products. In terms of surface area, this is the largest project in Marel’s history.
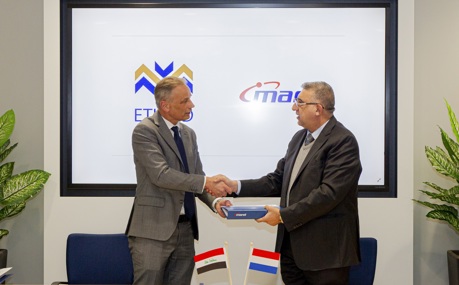
Two full-blown 15,000 bph lines
The four defeathering lines include four AeroScalders. Etihad particularly likes the AeroScalder for its absence of a shared water bath, avoiding cross-contamination, for its ability to precisely scald ‘white’ chicken and for its water and energy saving characteristics.
After a four-stage plucking process, the 7,500 bph lines are merged again into two full-blown 15,000 Evisceration lines. All conceivable pre- and post-eviscerator equipment is present here, with the Nuova 24 eviscerator taking center stage. The evisceration process is concluded with inspections, washing, pre-chill weighing with SmartWeigher and finally transfer to the chilling line via the LineLink EC.
Etihad has opted for a fully automated giblet handling process with Marel’s MG-150 (gizzards), PLH (livers) and HLS (hearts) systems. These giblets are air-chilled and then packed with four Multihead Weighers. A complete Feet Processing System, including Selective Foot Unloader, Paw Cutter, Feet Scalder, Feet Skinner and Feet Chiller, is also integrated twice.

Air chilling
In the meantime, the carcasses undergo in-line electro-stimulation, to end up as the most tender meat. The shock-maturation air chilling also plays an important part in tenderizing the meat. Etihad preferred a single-layer air chilling configuration, just to be absolutely sure not to have any dripping products on each other. This means that two enormous buildings are required just to house the two separate 15,000 bph air chilling lines, but that was no objection for Etihad.
Baby Line and parent stock
Etihad likes to give undersized, fragile products a dedicated treatment, apart from the automated process. For this purpose, the so-called baby line is a separate manual 1,000 bph processing line for very small chickens, installed in its own separate department. Prior to evisceration, these products are released from the regular line. The baby line features a manual evisceration process, which includes pneumatic scissors and a vent gun, and is finished with a screw chiller.
In a totally separate building, Etihad also processes parent stock. This 4,000 bph process makes use of a crate supply system, water bath stunner, water bath scalder, two-stage plucking and a fully automated Nuova evisceration process, followed by water chilling.
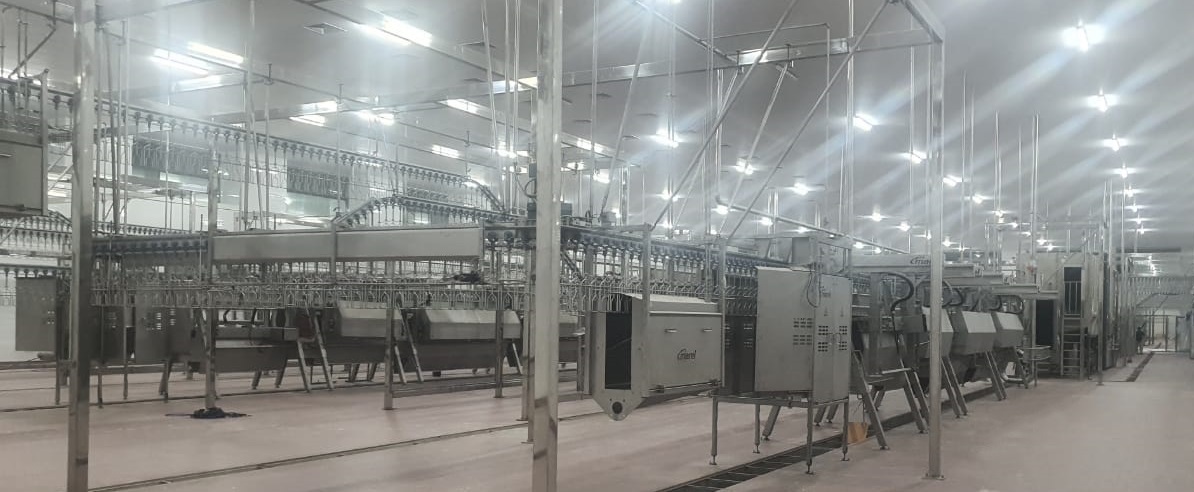
Whole products or cut-up
Although Etihad’s market is mainly about whole products, there is a significant amount of products among the 30,000 per hour to be cut up.
After chilling, IRIS systems and SmartWeighers decide, together with Innova PDS, which products can be packed right away (fresh or frozen, bulk, in bags, boxes, on trays) and which products can be cut up. Part of the non-chosen whole products are forwarded to a full-blown ACM-NT KFC line, including the typical keel bone cutter, to produce 8- or 9-piece bone-in products for QSR restaurants.
The other whole products enter two ACM-NT systems, starting with wing and breast cutters. The unloaded breasts are divided over four deboning systems, which harvest fillets and tenderloins in various combinations. Unloaded wings and deboned breast meat are directed to crate bulk packing or four calibrated tray packing lines, all including Multihead Weighers and MCheck2 checkweighers.
Leg meat
The ACM-NT line moves on to the leg cutters. Part of the bone-in legs, thighs and drums are forwarded to two Multihead Weighers and a tray packing line. The other legs, harvested by the JLR, pass on to a Thigh Fillet System. The boneless thigh meat is packed in catch-weight trays. The last remaining products in the overhead conveyor line are the drumsticks. They end up in two Marel DrumStick Deboning Systems.
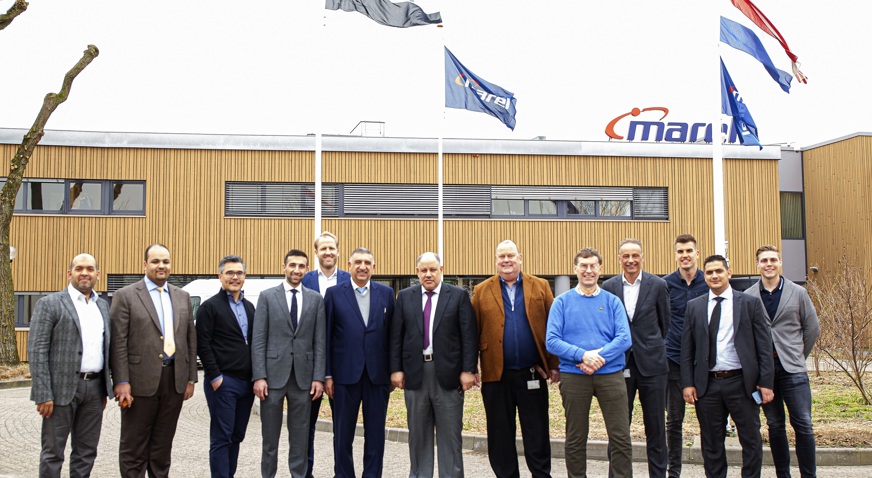
Further processing
Today, the market for convenience food in Iraq is dominated by imported products from Turkey, Ukrain, Jordan or Abu Dhabi. Etihad likes to play a role in this domestic convenience market too. That’s why the company decided to further process their poultry products with Marel.
First, the incoming products from the secondary process are treated in Marel’s Meat Preparation System, including the CombiGrind grinder and SoftMix mixer. Now the meat mass is ready for Marel’s 700mm Convenience Food Line. Etihad opted for the industry’s most flexible convenience food process, starting with RevoPortioner, which forms the desired end products. This can be popcorn, chicken kebab, chicken fingers, schnitzels or crispy burgers. The convenience line proceeds with Active Batter Applicator, Active Mixer, Active Tempura Applicator and two RevoBreaders. Thanks to their ability to change from drumbed to flatbed coating, two RevoBreaders together enable the creation of all sorts of end products on the same processing line while saving two extra machines that would be needed normally. It is easy to change from nuggets, needing flatbed coating only, to homestyle by opening the drum mode.
The coating line can also handle whole muscle products, after they’ve been portioned in an I-Cut 11 and split in a SmartSplitter. The Convenience Line is completed by a GoldFryer, ModularOven and two Multihead Weighers for packing.
The construction
Etihad is establishing a complete vertical integration on a monumentally vast site of about 565 km2 and in all areas, the company wants to have the best of the best. Hatcheries, feed mills and about 1,200 Etihad-owned chicken farms are built here, besides the processing plant.
Since medio 2022, huge progress in construction is being made and things go really fast. There’s a lot of determination in the company and Etihad has proven to be very capable in realizing their ambitions.
The tiling in the buildings deserves special attention. Millions of hexagonal tiles can be found all over the place, for example, in the new hatchery which is already completed. Tilers are having an enormous job in putting the millions of tiles.
In the processing plant all departments are immensely spacious, also because Etihad wants to have a machine-to-machine distance of at least 6 meters. This makes for a very clean, open factory design. Along all departments run side corridors with large windows, so everyone can see that Etihad is transparent about its activities. There are no secrets to hide. All corridors give a perfect overview of the crystal clear departments and make the buildings look like airport terminals.
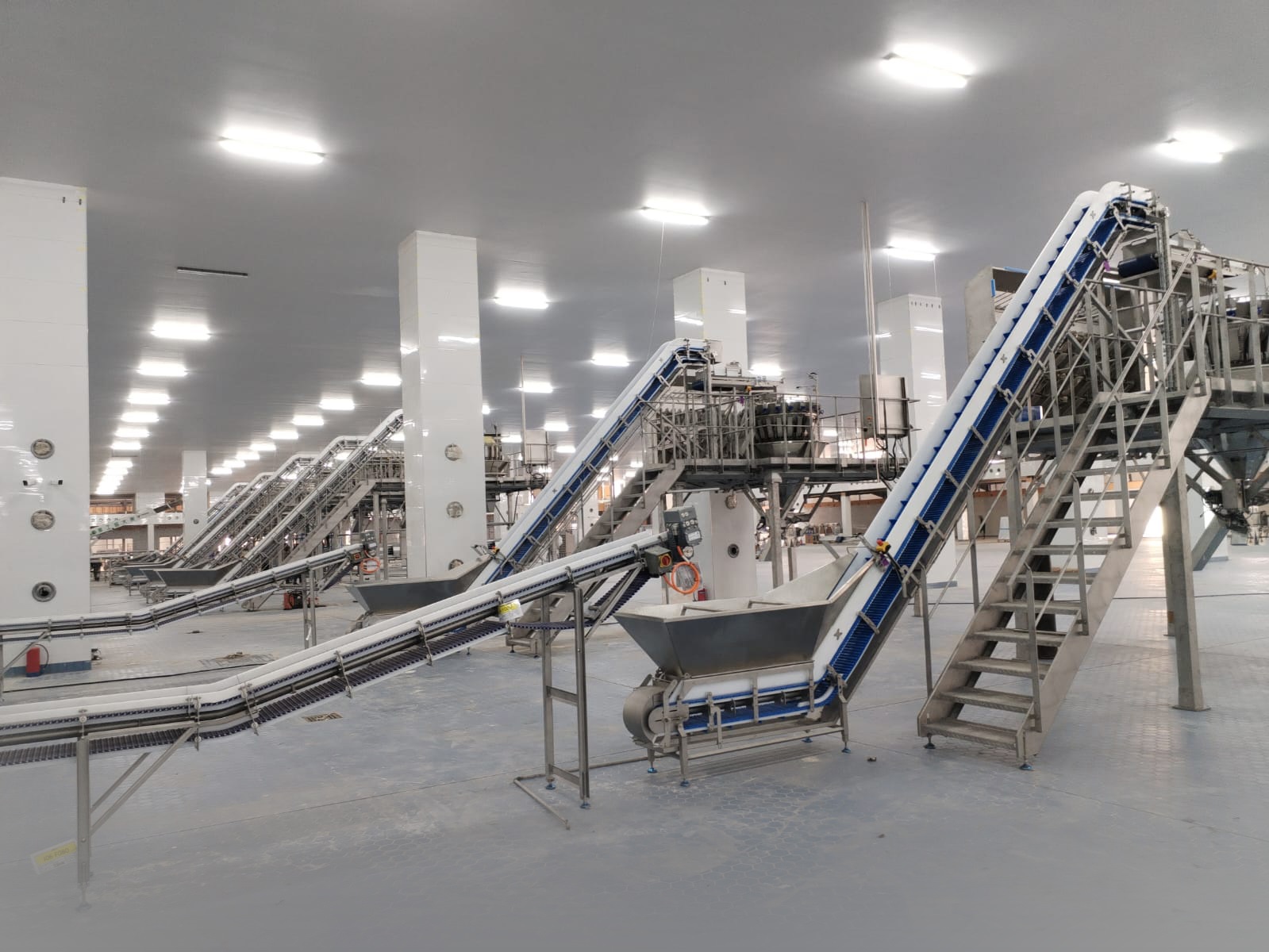
About Etihad
Established in 2012 at Medhatya region in the province of Babylon, Etihad’s production started with a sugar refinery. In the same area, Etihad established an edible oil refinery plant in 2016. The company owns a great fleet of 210 trucks and 100 tanker trucks which are deployed to transport raw cane sugar and raw oil from the port in Umm Qasr to the factories. Today, in the city of Babel, Etihad possesses two vegetable oil factories, a sugar refinery and a giant head office, which includes hotel rooms and spans about 1.5 km2. About 2000 employees work three shifts a day to have a 24/7 operation.
Another Etihad group is called Rayan. This branch includes a soybean extraction plant with a capacity of 3600 tons/day, a feed mill featuring six lines which produce 4400 tons/day and a Premix plant with 240 tons/day capacity. Etihad also possess concrete silo farms wich a storage capacity 720,000 tons of grains.
Etihad’s new 350 km2 site is located one hour outside the pilgrim city of Karbala in a further deserted area. There’s only one neighboring company, a Hyundai oil refinery, which makes it altogether an important economic zone for Iraq.
The giant site comprises many other industries besides Etihad’s poultry businesses. They got their own factory to construct sandwich panels on-site for all their buildings and farms. There’s no other way to get them delivered. Etihad also has its own tarmac factory to create the infrastructure, and its own powerplant for the necessary energy and cabling to every corner of the vast area.
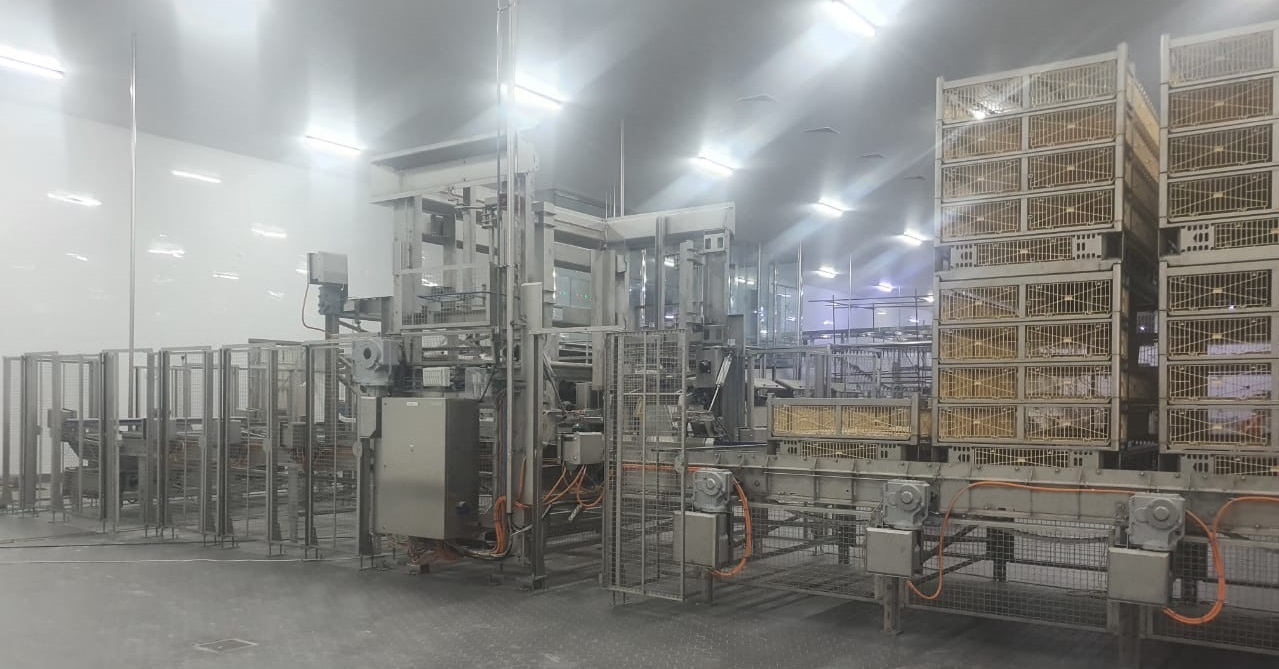
Get in touch
Our dedicated team is here to help and answer any questions you may have. Please complete the form, and we’ll get back to you as soon as possible. We look forward to hearing from you.